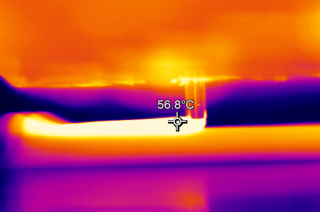
Project
Data-driven modelling and adaptive control of extrusion-based 3D food printing
This PhD project aims to develop models to predict printability of food materials, to reduce trial-and-error experiments and to investigate robust adaptive control to 3D-print a variety of food materials for product prototyping and personalized nutrition.
Current extrusion-based 3D food printing often focus on printing single-component food systems at room temperature. Achieving consistent and high quality of complex printed food products is still challenging but essential for commercial uptake of 3D food printing as a manufacturing technique. The low adaptability of the current food printing control system requires trial-and-error experiments prior to define the optimal process settings for printing new food materials. Improving the adaptability of the printing system will lead to precise dosing and smooth extrusion of complex food materials, which will ultimately benefit the stability and quality of printed foods.
Our goal
We aim to develop an adaptive printing control system for printing complex food materials with high accuracy and quality. We are integrating sensors (e.g. vision camera) into the extrusion system to monitor physico-chemical properties of food materials and printing quality. Data-driven models will then predict printing quality based on inputs such as specific printing conditions and properties of food materials. We will eventually develop a printing parameter recommendation system to best inform 3D food printing users for formulation development and printing optimizations of various food materials.
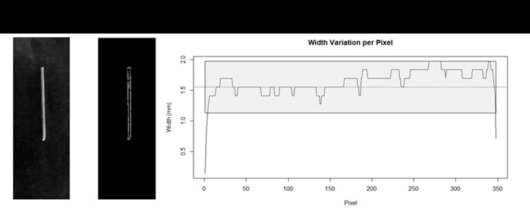
Illustration of first results: Image-based line filament extrudability assessment